Procesos de comunicación optimizados: Gestión de interrupciones en MAN Energy Solutions Schweiz AG, Zúrich
MAN Energy Solutions Schweiz AG (“MES”) y sus empleados fabrican turbocompresores para las industrias siderúrgica, petrolera y del gas en su planta de Zúrich. Ahora ha introducido una herramienta de gestión de perturbaciones con Simmeth.
Cada uno de estos compresores es un proyecto complejo con docenas de hitos, cientos de componentes, miles de pasos de trabajo y materiales necesarios. Para cumplir las normas de calidad más exigentes y los estrictos plazos de entrega, cada componente individual de la producción debe estar perfectamente integrado en el proyecto global. La más mínima desviación del plazo de un solo paso de trabajo puede poner en peligro el calendario global del proyecto. Por tanto, las contramedidas deben tomarse de inmediato, con determinación y en coordinación con los demás departamentos especializados.
Aquí es precisamente donde entra en juego la “gestión de interrupciones” introducida con éxito por MAN ES con la empresa de software Simmeth System en 2014. El objetivo del proyecto era optimizar los procesos de comunicación a nivel de valor añadido e informar automáticamente a los niveles estratégicos.
El proceso de la variable perturbadora
¿Cómo funciona un proceso así en la práctica? Es muy sencillo: si un empleado de un departamento se da cuenta de que no se puede cumplir un plazo previsto, por ejemplo porque un material no llega a tiempo, introduce una solicitud de reprogramación con una nueva solicitud de plazo a través de una pantalla de entrada en la herramienta de planificación wayRTS. Entonces se crea automáticamente una “variable de perturbación” en la base de datos central. A continuación, se envía inmediata y automáticamente un correo electrónico al planificador responsable de este proyecto con la información pertinente. El planificador aprueba o rechaza la nueva cita con un clic del ratón. Los departamentos responsables son informados inmediata y automáticamente por correo electrónico desde la base de datos y pueden reaccionar sin demora. Se documentan las causas de la interrupción y las razones de las respectivas decisiones. Esta documentación es el requisito previo para un proceso de mejora continua. Todos los pasos de la comunicación se registran en la base de datos y se procesan automáticamente en informes. Sirven de base para las reuniones periódicas desde el nivel de taller hasta la reunión semanal de directores de división y el informe a la dirección.
El proyecto
El proyecto se realizó con el “SC-Communicator”, un módulo de la solución de software “SC-Manager” de Simmeth System. SC-Manager” es una solución de base de datos centralizada para controlar la cadena de suministro. Se integra en el entorno informático existente e intercambia datos permanentemente con los sistemas ERP, de control de producción y de planificación.
“Más de 250 empleados acceden ahora al sistema de gestión de interrupciones como herramienta central de comunicación para la creación de valor”, dice Michael Budimir, Jefe de Planificación de MES. “Se ha optimizado el proceso detallado de planificación y aprobación de la creación de valor y se ha creado una herramienta de información para todos los niveles jerárquicos, desde los planificadores hasta la dirección”.
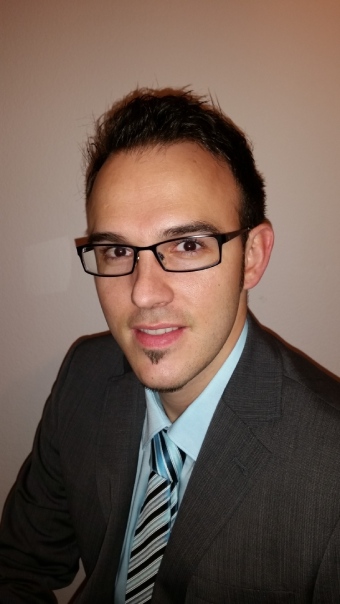
Informar
Por último, pero no por ello menos importante, los informes 100% automatizados permiten obtener informes y KPI en cualquier nivel de agregación con sólo pulsar un botón. Este proyecto no sólo garantizó el retorno de la inversión en muy poco tiempo, sino también una mejora sostenible del proceso en los años venideros. Gracias a los informes generados automáticamente y a los datos directamente disponibles, las reuniones de los directores de división se celebran ahora con mucha más frecuencia que antes.
Conclusión
El Dr. Christian Lazar, Director Financiero de MAN Energy Solutions Schweiz AG, resume: “Los problemas del proceso pueden medirse de forma transparente con las herramientas que se han introducido. Cualquier problema puede medirse en tiempo real. Sobre la base de los hechos analizados, se pueden orientar e implantar inmediatamente mejoras en los procesos.”
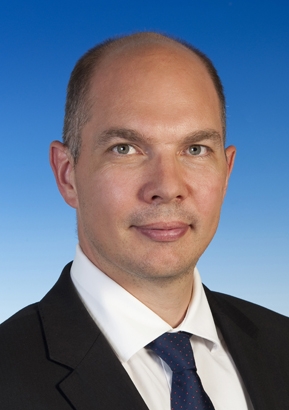